Coffee Roasting
Cost and Inventory Traceability from Beans through Packaged Blend
Here is how large volume Roasters use DataNinja with QuickBooks Online to run their operations with clarity.
1. Purchase Green Beans
Record the purchase transaction in QuickBooks (usually a Purchase Order). This purchase transaction must be made using an Inventory Item or Inventory Part for the specific Green Bean.
2. Receive, Barcode, Inspect
When inventory is received, a unique barcode identifier tracks: Lot Number, Supplier Shipment, Purchase rate per lb/kg, Quality Release Status, Expiration Date, and Location.
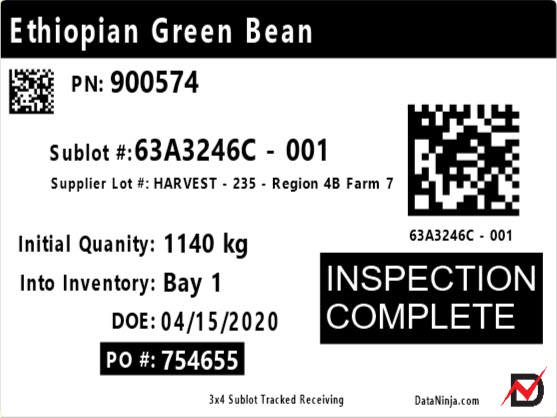
Example Green Bean Inventory barcode with Identifier.
This identifier is used for traceability and loading the material costs of the actual green beans into the roasts and blends they will produce.
Landed Cost
Sometimes you won't know your full cost of the beans until they arrive. You can load freight and import fees into the applicable inventory receipt so tracking costs downstream is fully burdened with landed costs.
When a quality inspection of the green beans has been completed, the system will allow consumption of the raw material.
3. Roast & Grind
Add Roasting to the Production Schedule. In the electronic manufacturing record, operators use mobile devices to scan green beans entering the process. After the roasting step is complete process workers will record the yield weight. DataNinja logs the variances automatically.
When yield is recorded a new barcode is generated to track the downstream usage of the roast.
4. Blend/Package
Combining multiple blends and packaging variations together to produce finished goods is usually recorded in a separate manufacturing record from the roasting step. Operators scan the roast identifiers (Lot/Batch Numbers) as they are loaded into the process. Operators also verify the quantity of packing components used. Completion of the manufacturing record creates an actual cost tier for the finished good in QuickBooks. This cost is based on the raw material costs, roasted costs, Material variances and direct labor/overhead.
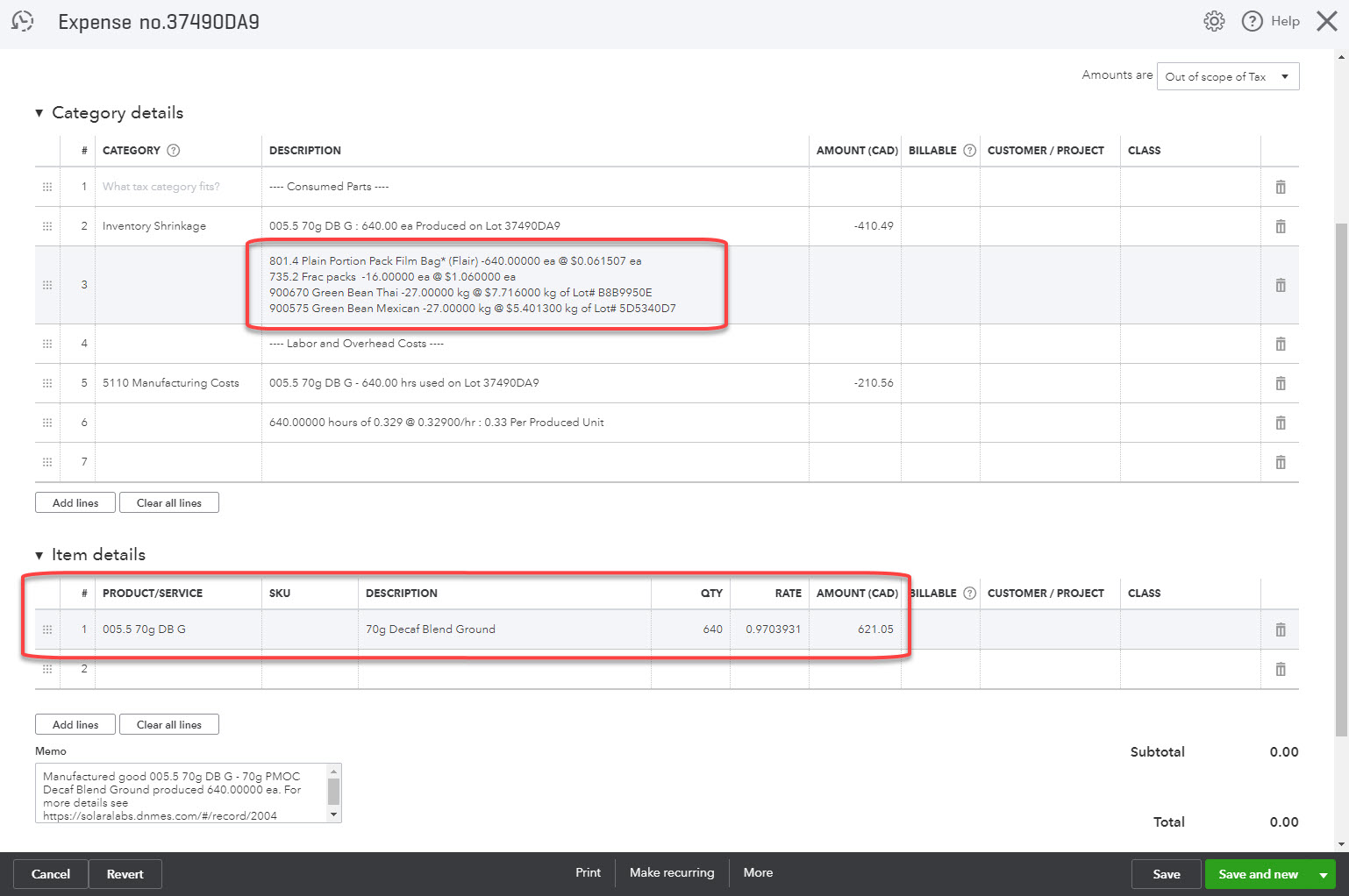
Actual inventory costs of roasted blends and packaging flow into the finished good cost.
When finished good yield is recorded, a barcode is generated to track warehouse movements and shipment of the finished goods.
5. Fulfill
Scan the batch number into a customer order and fulfill with packing list attached to invoice in QuickBooks. When shipment is complete the actual costs hit COGS and margin analysis data is available for reporting and trending in both DataNinja and QuickBooks.
QuickBooks Online vs QuickBooks Enterprise Desktop
The same functionality is available for both
Updated about 2 months ago