Equipment Management
Electronic Equipment Management with DataNinja
Tracking equipment can help streamline service request processing, lower equipment cost, and help operations staff use the right equipment, at the right time, for the right job.
Automatic Calibration Checks
Equipment calibration and operational status are verified in real-time whenever equipment use is
recorded. Have confidence that the corresponding quality documentation is well defined, completed, and up-to-date.
To get to this page select the gear icon in the top left of your browser then under Tools select "Equipment".
Set and Enforce Maintenance Intervals
Set regular intervals for required maintenance that are unique to each asset. DataNinja equipment management provides a platform for your staff to report equipment concerns the moment they arise.
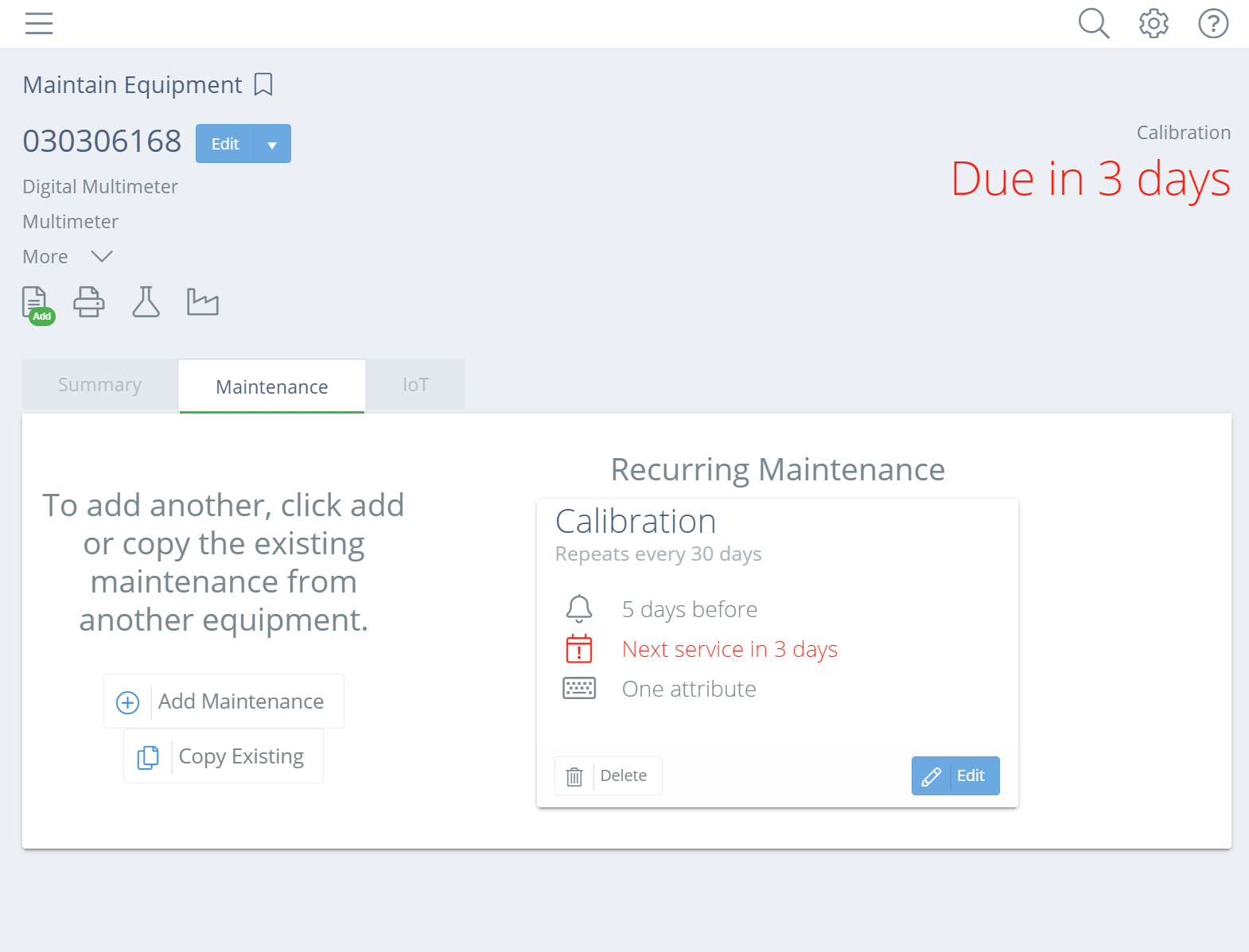
To add a maintenance interval simply select the maintenance tab of the selected equipment to either copy an existing interval or to add/create a new interval.
Complete, Single Source of Truth
Manage all interactions between staff and equipment a single place. DataNinja keeps your change history organized and granular permissions allows appropriate access to 3rd party technicians.
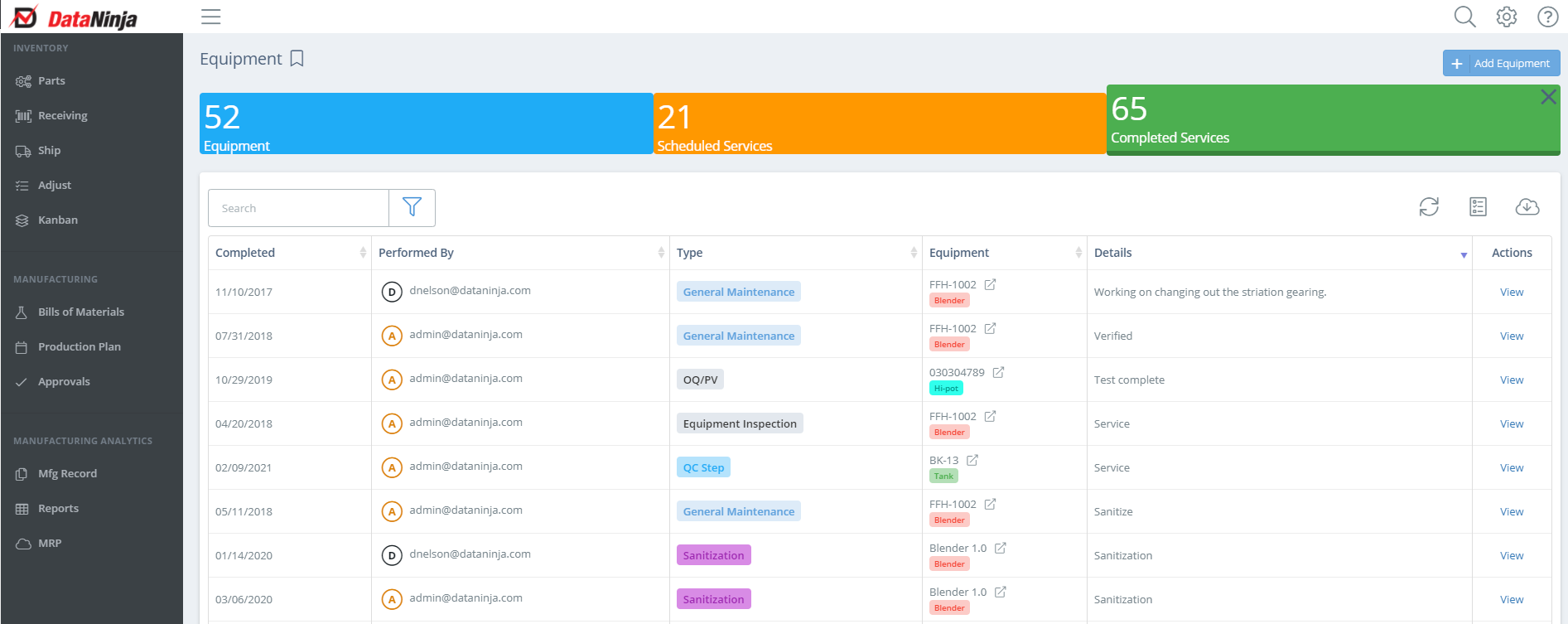
Go to the equipment page and select the top left "Completed Services" tab to see the comprehensive history.
Manage with a Scan
Each asset is uniquely tracked by serial number in DataNinja. Navigating to equipment details or recording service is easy to do from a mobile device and 2D barcode scanner.
Connected Equipment IoT
DataNinja connects your production equipment to the cloud. Connect data equipment results and history directly to the relevant quality records. A robust industrial internet of things connection is available to all of your equipment through DataNinja equipment management via the DataNinja Hub.
Updated 3 months ago