Shelf Life Days
How inventory's default expiration date is calculated.
Shelf Life Days
Shelf life (stored in days) is a Part Master Data setting that is only available on Batch or Sublot Tracked Items. At the time a new item is created this setting is set to 0 or “Never Expires”. Part tracked only items, only have their location and quantity tracked and cannot have any kind of shelf life captured or enforced.
The “Shelf Life Days” Part Master Data setting is used to calculate the defaulted in expiration date when a new lot is created (when an Item is received or a manufacturing job is scheduled).
For Example:
If a sublot tracked part has a “Shelf Life” of 30 (days) is received today, the expiration date default will be calculated as todays date +30 (days).
If a sublot tracked part has a “Shelf Life” of 45 (days) and is scheduled for manufacture next week, the expiration date is calculated as the scheduled Date of Manufacture + 45 (days).
Part Tracked Inventory
In Data Ninja anything that is Part tracked cannot have an expiration, or as we call it “Shelf Life”, associated with it.
Adding Shelf Life Days
When creating or editing a Parts Master Data select the data field next to "Expires" input the amount of days from either receiving or production of when you want this part to expire.
The "Date of Expiration" recommended based on the part master data settings can be overridden at receiving or during production planning BEFORE any labels are printed (preventing relabeling).
Any changes performed POST receiving (barcode label printing) OR mid-way through manufacturing CAN be performed by a DataNinja User with the “Maintain Batch >> Update date of expiration” permission. Even though the software controls are enforced regardless we strongly recommend that inventory control tags be reprinted and applied if the human readable date of expiration is present.
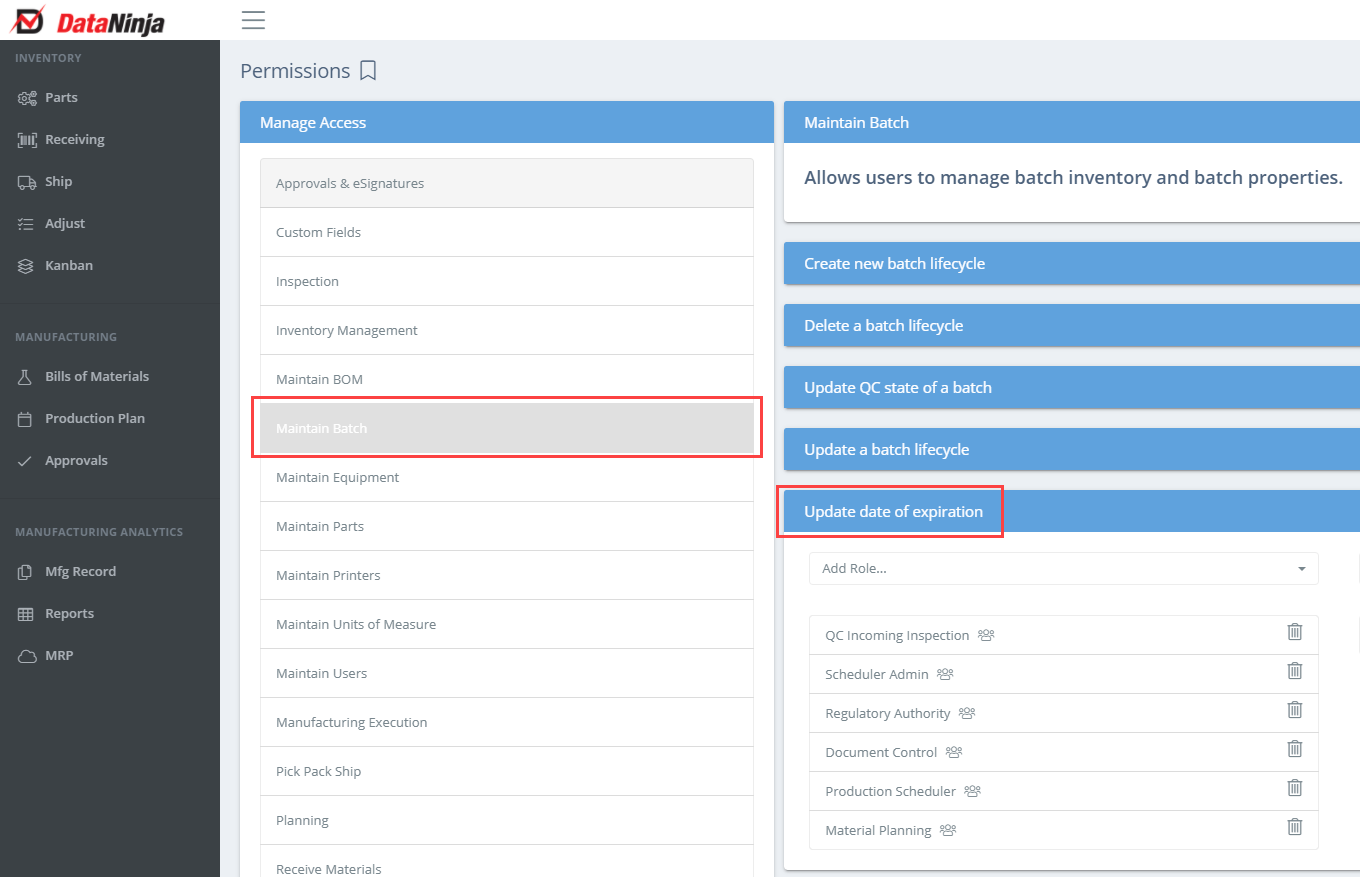
Permissions required to update date of expiration for products once the label has been printed.
Updated over 1 year ago