Default Shelf Life
For parts that can expire, set up Shelf Life to prevent using or shipping any bad product.
Auto-verification can alert operations if bad product is about to be consumed or shipped to fulfill a customer order.
Shelf life determines the default number of days past inventory creation that the inventory of a part can be consumed or shipped. Setting up Shelf Life is useful when you want to minimize repetitive data entry during inventory receiving or production.
How to Set a Part's Shelf Life
Click into an existing part and select Edit, or begin creating a new part. Next, find the Expires field beneath the Part Classifications section. If the part never expires, don't make any changes to the field. The default expiration is Never.
Once you click on the Expires field, the field will now show as Shelf Life.
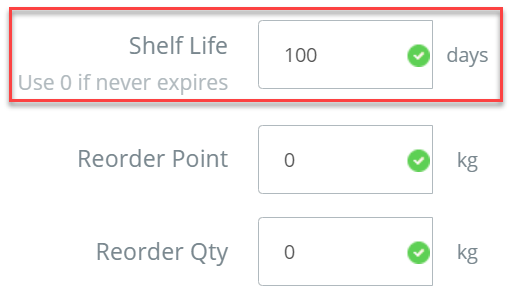
Shelf Life for Raw Materials vs. Finished Goods
Raw Materials: A Shelf Life of 400 days for a Raw Material means that if you accept the default expiration date at receiving, the Shelf Life will be exactly 400 days from the day it is received (when the barcodes are printed).
Finished Goods: A Shelf Life of 90 days for a Finished Good means if you accept the default expiration date in the manufacturing record, the Shelf Life will be exactly 90 days from the moment the Finished Good is made (when the barcodes are printed).
How will it look on a daily basis?
At Inventory Receiving:
When staff are receiving raw materials, the part's Shelf Life will be added to the current date and defaulted into the Expires field.
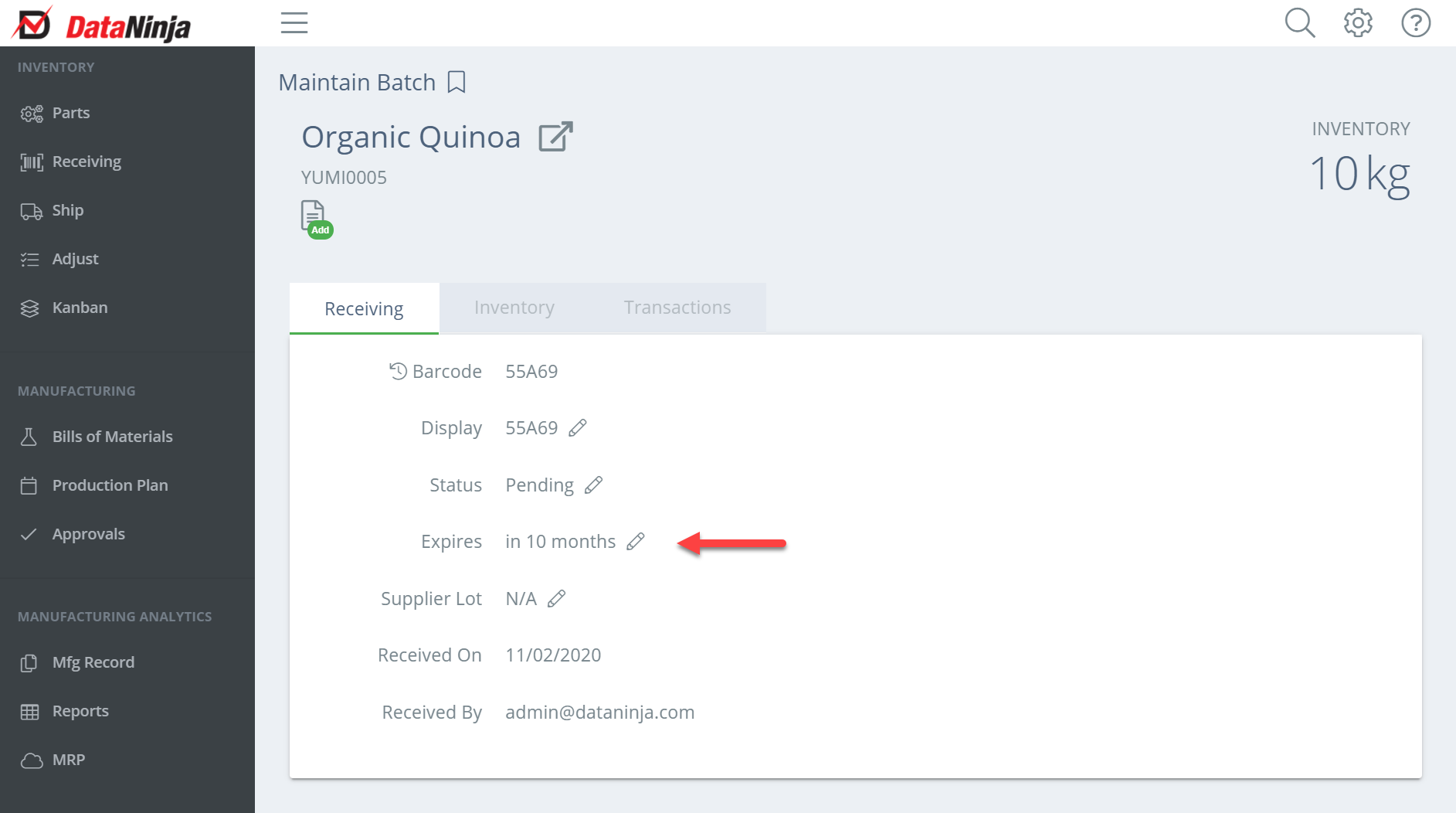
The operator can record the true expiration date if it is different than what the default shelf life helped calculate, by selecting the pencil icon next to the expiration date.
Produced Inventory (Finished Good or Sub-Assembly):
Similar to how Shelf Life works at inventory receiving, in a manufacturing record the Production Manager can specify the system expiration date for produced WIP or Finished Goods by selecting the pencil icon next to the date of expiration field.
Updated 24 days ago