Bills of Materials (BOM)
Where it all comes together!
Anything you want to track inventory of needs a part number. The part number uniquely identifies what the inventory is, while the BOM tracks the "recipe" for how to make the inventory, if a particular part is generated via the consumption of other parts (like a Finished Good or Sub-Assembly). The BOM number is where you specify how inventory of a produced part comes into existence.
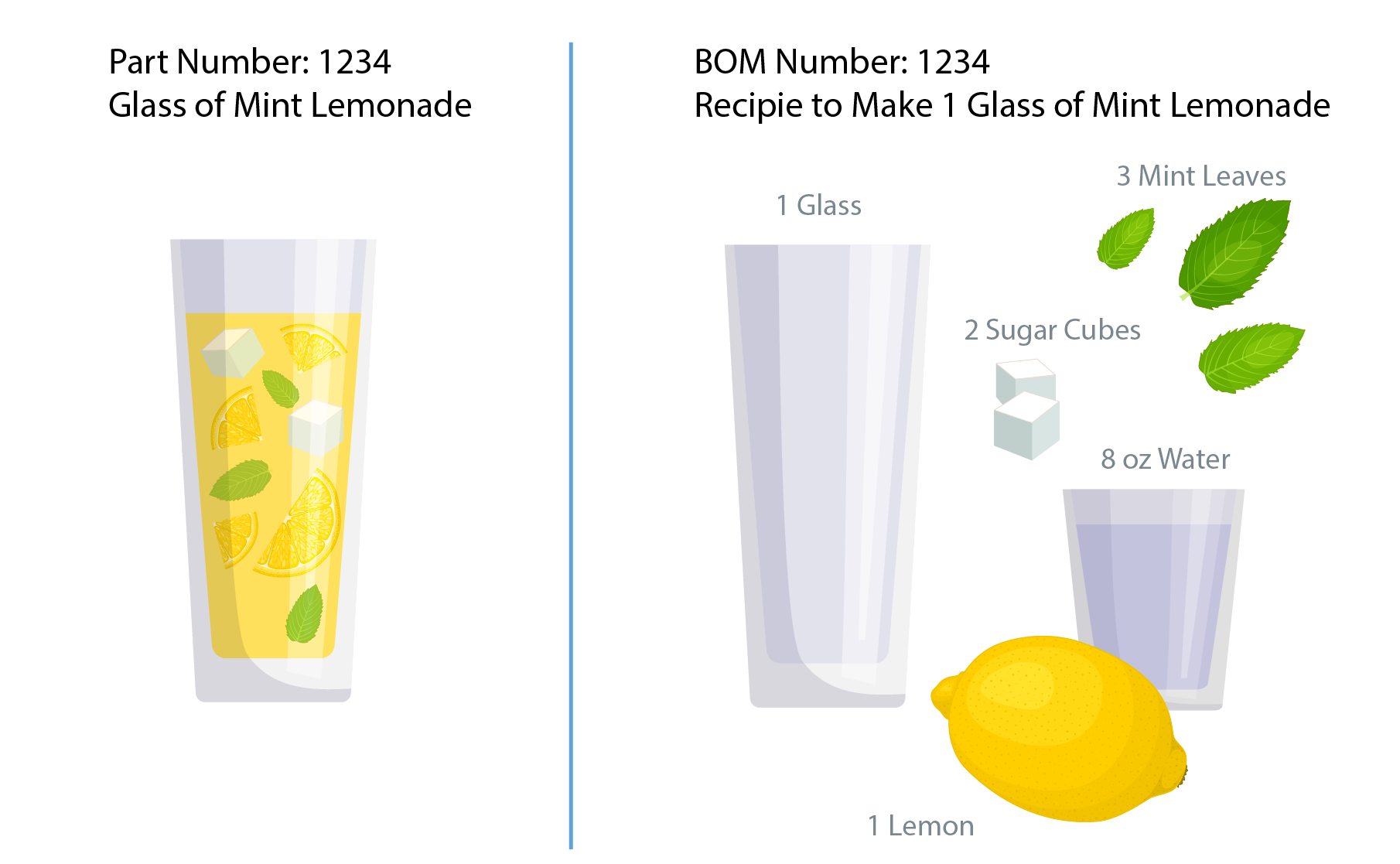
The BOM number is the part number that is produced whenever the BOM is followed
The BOM is where you can map your process into DataNinja so that you can control how the ingredients come together to produce inventory of a product.
Scalable and Repeatable
When fresh inventory of a part is generated via the consumption of one or several other parts, a Bill of Materials (BOM) is used as a repeatable, scalable way to handle the inventory transactions and control the process.
A DataNinja BOM contains:
- Configuration
- Required parts
- Attributes (customizable data collection and verification web-form building blocks)
- Approvals
- Equipment
Lingo
Depending on your business processes, one or more of the following terms may be synonymous with what DataNinja means when referring to a BOM: Recipe, Formulation, Routing, MMR etc.
Creating a New BOM
BOMs Should Be Created in NetSuite
All BOMs should initially be created in NetSuite and synced to DataNinja. Once the BOM is in DataNinja, additional changes can be made to it. Do not create new BOMs in DataNinja if your company uses NetSuite.
Additional Fields on BOMs
By opening the BOM and pressing "Edit", then expanding the "Additional Fields", you can specify the following:
- Default Batch Size
- This specifies the default quantity to produce when the BOM is used in a production order. The standard default is 1, but if following this BOM will typically create a greater or lesser quantity of the part, then adjust the number accordingly. This field uses the same Unit of Measure (UOM) as the part. If it is incorrect, make the adjustment at the part level before creating the BOM.
- Minimum Quantity
- This specifies the minimum quantity that you can schedule to be produced. The standard default is 1, but if the Default Batch Size is greater than 1, you can adjust the Minimum Quantity to be greater than 1, so long as it is less than or equal to the Default Batch Size. This field uses the same Unit of Measure (UOM) as the part. If it is incorrect, make the adjustment at the part level before creating the BOM.
- Maximum Quantity
- This specifies the maximum quantity that you can schedule to be produced. The standard default is 1000, but can be adjusted as long as it is greater than or equal to the Default Batch Size. This field uses the same Unit of Measure (UOM) as the part. If it is incorrect, make the adjustment at the part level before creating the BOM.
- Location
- The standard default is the location associated with the part. This is where inventory will be produced into once the BOM is used in production.
- Customer
- If this part is going to be sold or shipped directly to a specific customer, you can specify which customer in this field.
- Variance
- The standard default variance is between 90 and 110 percent. Going above the maximum or under the minimum will trigger an escalation. The percent is based on the Default Batch Size. You can adjust both the upper and lower limits, if you need to be more or less strict about the amount produced in an order.
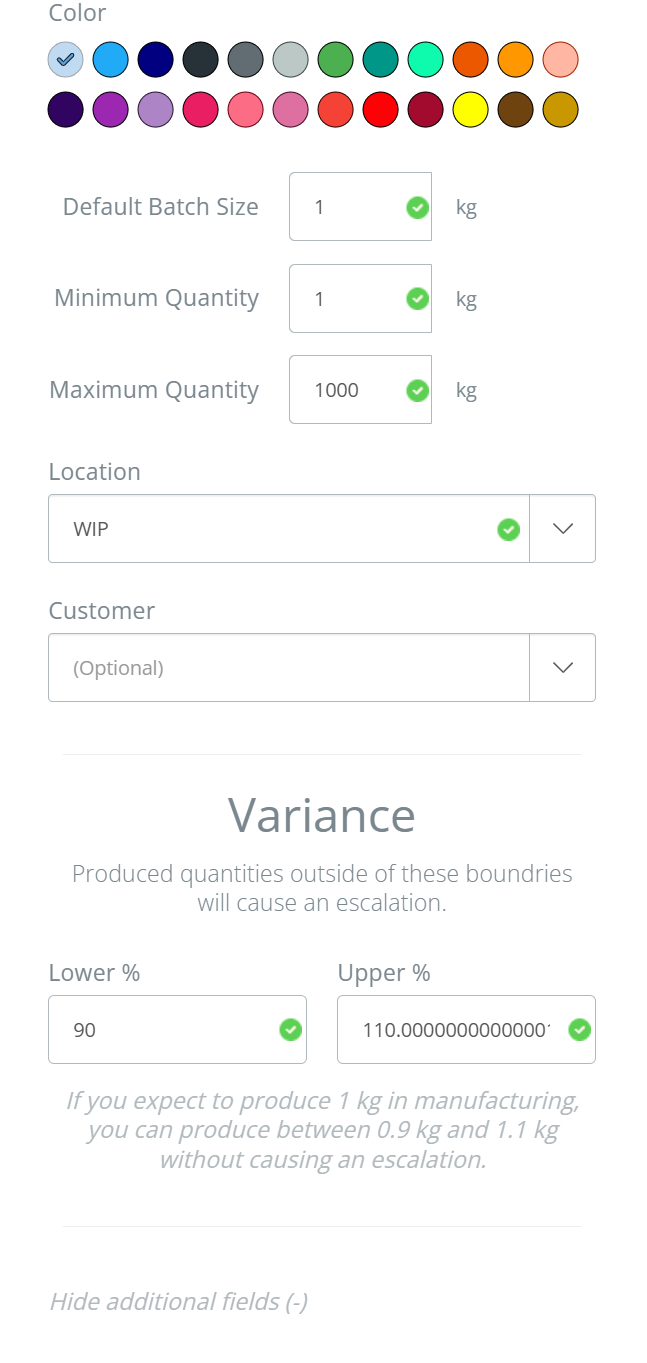
Releasing a BOM
Now that your BOM is complete, setting the BOM's Lifecycle to "Released" will make it possible to schedule the BOM on your production plan.
From the "Edit BOM" view. Toggle the Lifecycle to "Released" near the top right of the screen.
Scheduling Production
Select "Production Plan" from the left sidebar, then click "Add to Schedule".
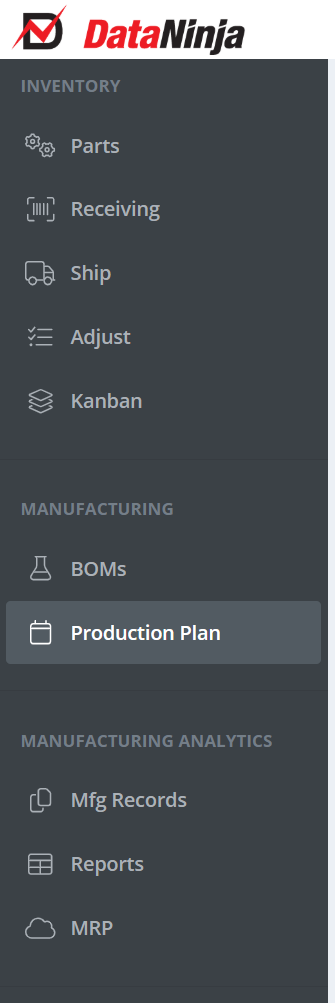
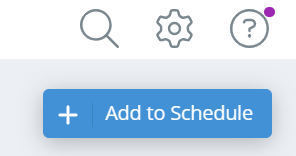
For more details, see Scheduling Production.
Updated 3 months ago
BOM Configuration Settings